GOMA uit Hengelo is een internationaal georiënteerde toeleverancier gespecialiseerd in hoogwaardige plaatwerkproducten, zowel halffabricaten als ook complete producten. Met Co-creatie, het gebruik van volautomatische plaatbewerkingsmachines, las- en puntlasrobots, een eigen poedercoatinstallatie en montagemogelijkheden bieden ze meerdere mogelijkheden voor onder andere de productie van behuizingen en omkastingen. GOMA is in 1962 opgericht en is in die jaren gegroeid tot een bedrijf met 120 medewerkers.
Efficiency op de productievloer
We bespreken de ontwikkelingen van de laatste jaren bij GOMA met Mark Oldenhave, procesengineer en productieplanner bij GOMA en Jorg Jolij, 3e jaar student Technische Bedrijfskunde en in dienst bij GOMA als stagiair. Mark legt uit dat GOMA de laatste jaren te maken heeft gehad met een teveel aan voorraden. Voorraden kregen een plekje op de werkvloer waardoor er minder overzicht was, wat ten koste ging van de efficiency en productiviteit.
John van den Boomen, organisatieadviseur bij SpartnerS, werd gevraagd om te ondersteunen in de verbeterslagen die ze wilden maken. Bij de start werd samen met de Managing Director en Manager Operations van GOMA bepaald welke projecten als eerste aangepakt moesten worden. Mark: “Aan de hand daarvan zijn er verschillende teams samengesteld om met de betrokken medewerkers gericht aan de slag te gaan.”
Klantorder gestuurd werken
De oplossing voor de vele voorraden lag in de transformatie van GOMA naar een klantorder gestuurde organisatie. Mark: ”Productieorders worden nu uitgegeven aan de hand van klantprognoses. Daardoor lopen de voorraden en het onderhanden werk niet op.” Om dit te realiseren heeft GOMA een afdeling planning opgezet die de vraag naar producten goed in de gaten houdt.
De oplossing voor de vele voorraden lag in de transformatie van GOMA naar een klantorder gestuurde organisatie.
Lay-out aanpassingen
Daarnaast werd er gekeken naar de lay-out van de fabriek. Waar het eerder niet precies duidelijk was waar voorraden zich bevonden, is er nu overzicht gecreëerd door vakken voor tussenvoorraden te plaatsen en stellingen weg te halen. Dé manier om wijzigingen aan te brengen in de lay-out, is om het stapsgewijs te doen, aldus Jorg. ”Het is een grote hal. Als je begint met eerst een of twee afdelingen te veranderen, dan kun je op basis van voortschrijdend inzicht daarna de volgende stap nemen. Zo blijft het qua hoeveelheid werk ook te overzien.”
QRM
Op het moment dat de klantorder gestuurde organisatie stond, is gestart met het inrichten van QRM cellen op zowel het kantoor als op de werkvloer. Uitgangspunt was het verkorten van de interne doorlooptijd en het terugbrengen van het onderhanden werk. Jorg: ”Door te werken met QRM cellen kun je opeenvolgende processen bij elkaar brengen. Zo ging bijvoorbeeld eerder het product na het kanten nog op een pallet naar de montageafdeling. Nu worden de bewerkingen in één cel gedaan, dat is een stuk efficiënter.” Het werken met QRM cellen heeft voor een aantal artikelen een doorlooptijdreductie van 8 naar 1 dag opgeleverd.
In onderstaand processchema zie je hoe de doorloop in de productie gewijzigd is:
QRM wordt inmiddels voor een aantal producten toegepast. Ook hierbij is gekozen voor een stapsgewijze implementatie, zodat de productie altijd kan doorgaan. Jorg: ”Het stapsgewijs werken heeft ook als voordeel dat we de testopstellingen tussentijds kunnen aanpassen. En met deze goede resultaten kunnen we andere producten ook aan deze manier van werken toevoegen.” De verbeteringen zijn een samenspel tussen het projectteam van GOMA en organisatieadviseur John van den Boomen.
Aanpak en voortgang
Als begeleider van alle projectteams komt John eens in de twee weken een dag naar GOMA om de voortgang door te nemen met de teamleden. ”Dan bespreken we de status van het project en maken we samen nieuwe plannen”, vertelt Mark. Die plannen worden meteen omgezet in nieuwe acties en ter plekke wordt ook bepaald wat er de volgende keer op de agenda komt te staan als het projectteam en John bij elkaar komen.
De werkwijze van John is erop gericht om de mensen op de werkvloer erbij te betrekken om mogelijke weerstand tot veranderen zoveel mogelijk weg te nemen. Jorg: ”John zorgt ervoor dat de ideeën van de medewerkers worden meegenomen. Waarom voor iets gekozen is, wordt altijd goed uitgelegd en toegelicht, zodat ze snappen waarom het op deze manier gebeurt. Daarnaast betrekt hij hen bij de inrichting van hun eigen werkplek. Dat is denk ik waarom het medewerkers motiveert om mee te gaan in de veranderingen.”
De ideeën van de medewerkers worden meegenomen.
Draagvlak
Het bedrijf breed spelen van het QRM spel is één van de methodes geweest om draagvlak te creëren binnen de organisatie. Bij dit spel worden op een eenvoudige manier de principes van QRM uitgelegd waarbij je tevens direct de resultaten ziet die QRM kan opleveren. Inmiddels hebben zo’n 70 medewerkers het spel gespeeld. Jorg: ”Op de werkvloer zijn de mensen vooral bezig met de uitvoering van hun werkzaamheden en niet zozeer met processen. Met dit spel laat je deelnemers zien wat een andere manier van werken allemaal kan opleveren.”
Doorlooptijdverkorting
De eerste resultaten waren al snel zichtbaar: de productiviteit steeg en het overzicht op de werkvloer kwam weer terug. Er hoefde minder gezocht te worden, de tussenvoorraad bleef beperkt en er was weer structuur op de afdelingen. De hoge voorraad werd afgebouwd waardoor de kosten verlaagd werden. Daarnaast is de gemiddelde doorlooptijd in de fabriek, onder andere door QRM, inmiddels teruggebracht van 6 weken naar 3 weken.
”Doordat we nu klantorder gestuurd werken en alles plannen, hebben we veel meer controle op onze productie. Niet alleen is het aantal spoedjes veel minder, we zijn nu ook echt aan het produceren wat nodig is, Dat betekent alleen nog waar de klant om vraagt en niet om voorraden op te bouwen”, aldus Mark.
De gemiddelde doorlooptijd in de fabriek is inmiddels teruggebracht van 6 weken naar 3 weken.
Samenwerking
John is inmiddels al een aantal jaar betrokken bij GOMA en Mark denkt dat hij nog wel een aantal jaar zal blijven. Daarin zie je dat er een duurzame samenwerking is ontstaan. Mark: “John weet er veel van en kan het goed overbrengen. Ik kan heel fijn met hem samenwerken en heb veel van hem geleerd.”
Jorg: “John is toegankelijk en dat helpt wel mee bij GOMA. Hij wordt op de werkvloer goed ontvangen en mensen zijn bereid om een praatje met hem te maken en dingen met hem te bespreken. Hij kijkt daarbij naar waar behoefte aan is en speelt daarop in. Ook legt hij mooi uit wat de te behalen resultaten kunnen zijn, waarom we de dingen op een bepaalde manier gaan doen en geeft daar dan de achterliggende theorie bij.”
Plannen komende jaren
GOMA gaat nu starten met het opzetten van een QRM straat. Jorg: “We noemen het een straat maar het is eigenlijk een hele grote cel, waar dus veel producten in geproduceerd kunnen worden.”
Op basis van de resultaten die ze door de verbeteringen van de afgelopen jaren zien zijn ze tevens aan het kijken of ze een nog betere goederenstroom door de productie heen kunnen krijgen als ze het nogmaals omgooien. Mark: “De poedercoat straat wordt nog wat aangepast en de expeditie gaat nog verder naar achteren. Wat betreft de lay-out gaat er dus nog wel het één en ander veranderen. Er gaan ook nog wel wat dingen verhuizen. Dat is wat er de komende jaren op het programma staat.”
Concluderend stelt Jorg: “De grotere stappen zijn denk ik al gemaakt. Maar het is vooral het finetunen waarin nog veel te behalen is.”
In dit voorbeeld las u waarom een ondernemer ervoor kiest om de beste kennis in huis te halen.
SpartnerS spreekt uw taal en komt met praktische oplossingen.
Wat zijn uw uitdagingen? Vertel het ons, wij luisteren.
Bel ons op 040-3034400, of mail naar info@spartners.nl
We komen graag met u sparren.
- Afname van de voorraden
- Overzicht creëren op de werkvloer
- Planning verbeteren
- Doorlooptijd verkorten
- Doorlooptijdreductie van gemiddeld 6 naar 3 weken
- Meer controle over de productie
- Afbouw voorraad waardoor kostenreductie
- Overzicht op de werkvloer en productiviteitsstijging
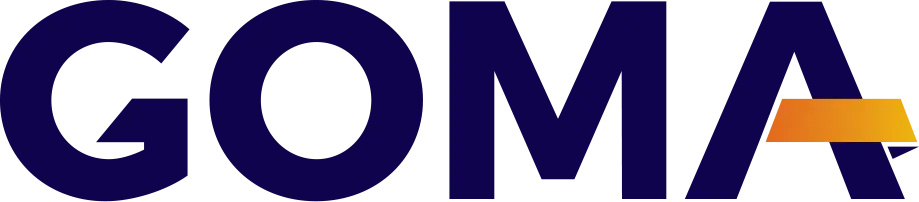
GOMA uit Hengelo maakt hoogwaardige plaatwerkproducten, zowel halffabricaten als ook complete producten.
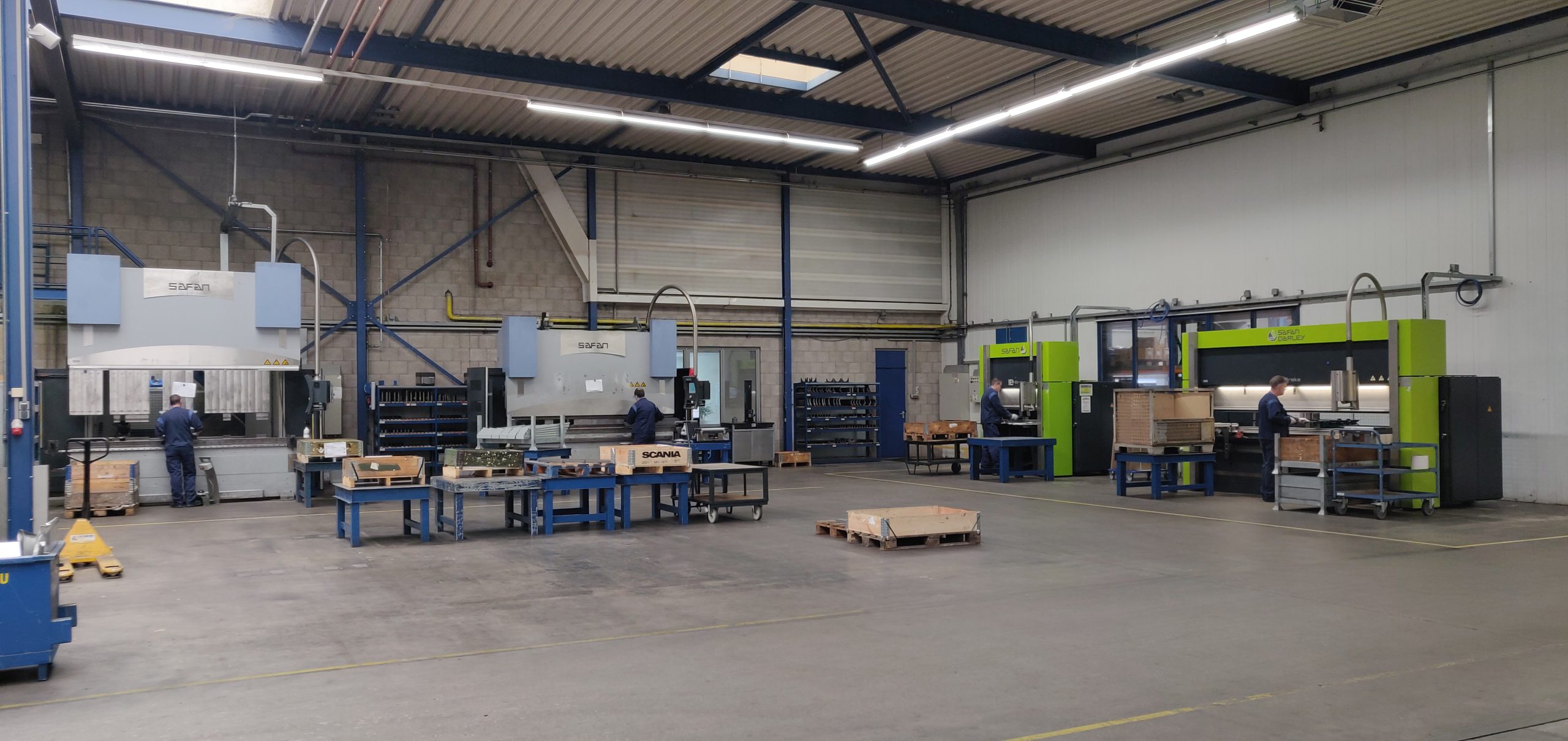